Unfolding the possible
We explore the tech universe to discover what’s next and build what matters.
Our mission?
Make the future closer, opening access to new frontiers in Space, Tech, Ventures.
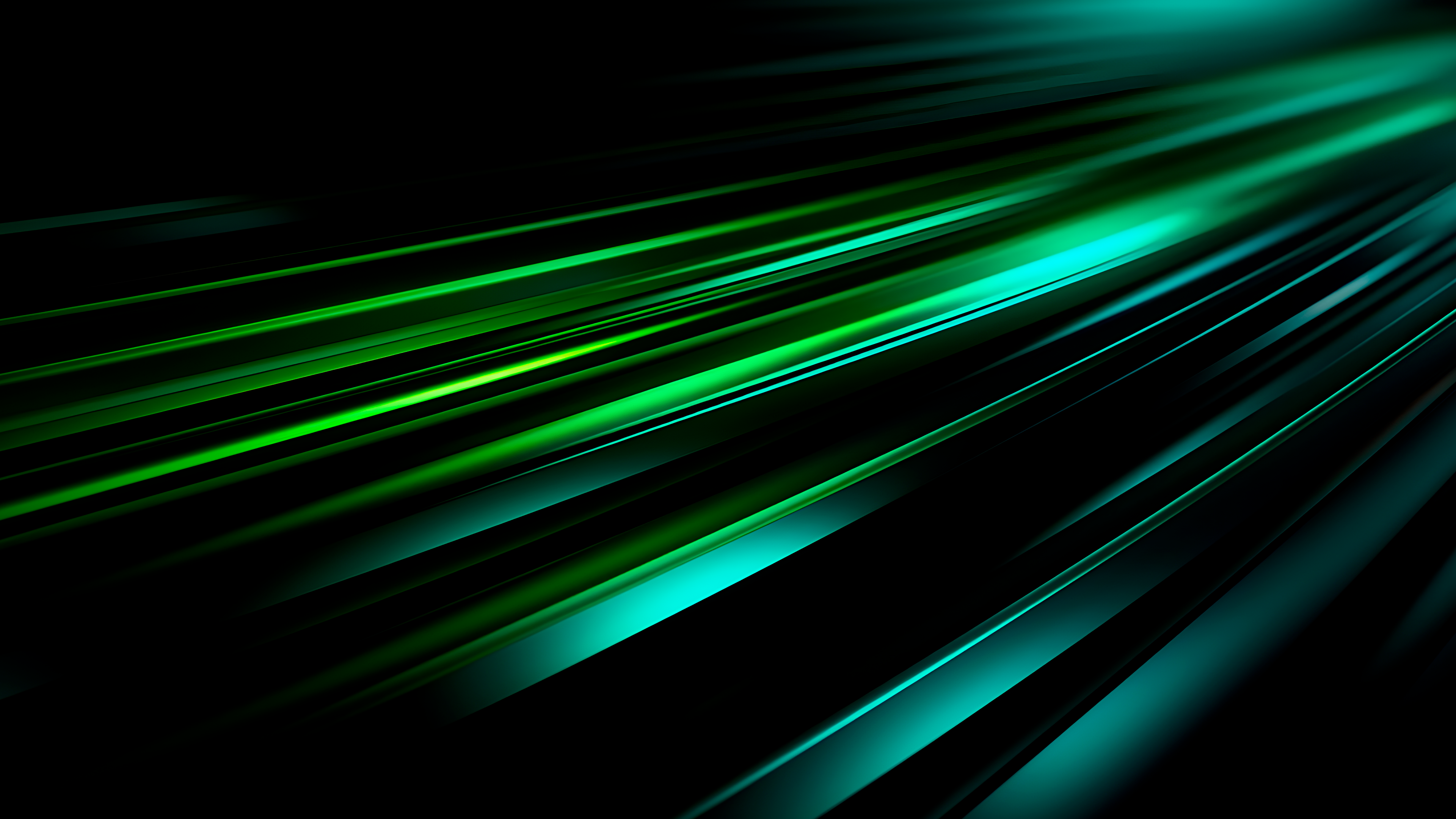
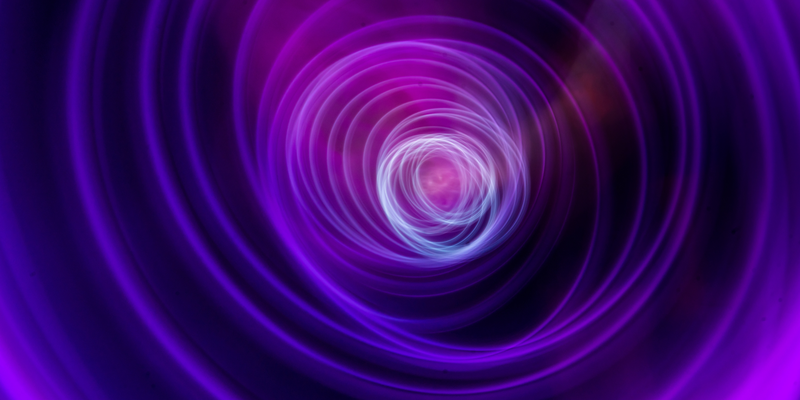
G-nous Space
We deliver multiple services, helping commercial and governmental sectors to explore disruptive opportunities in the Space market.
Go to Space
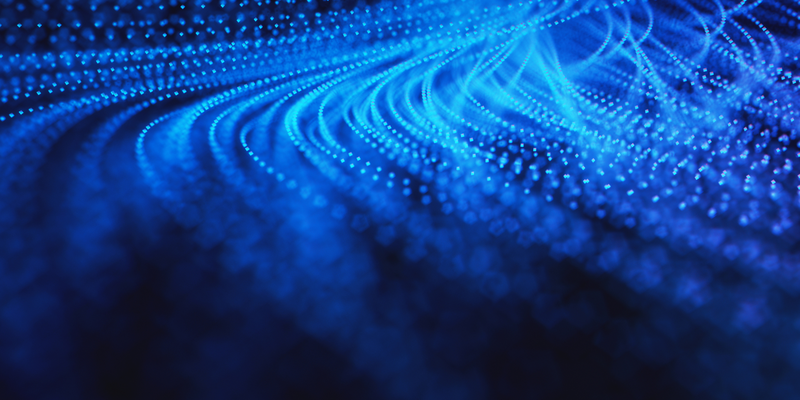
G-nous Tech
We enable businesses to harness advanced technologies and optimise their processes through robotics, AI and data science.
Go to Tech
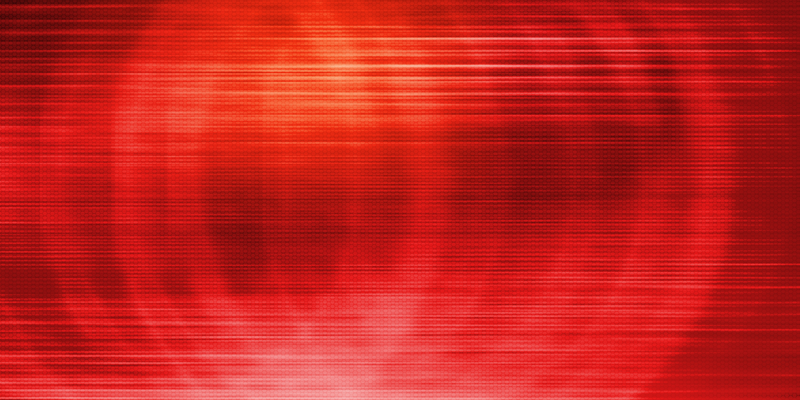
G-nous Ventures
We build innovative products and empower founders to unlock their full potential through our technologies and business model.
Go to Ventures
We are trusted by
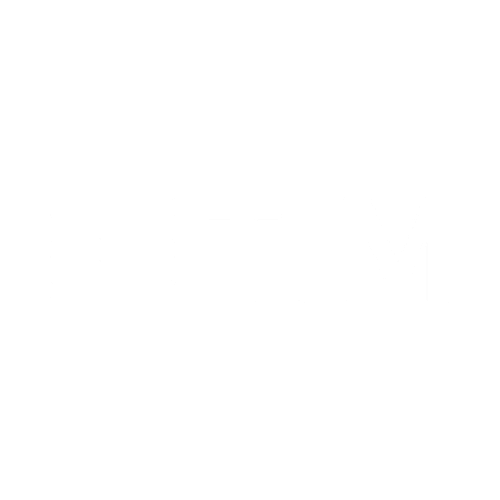
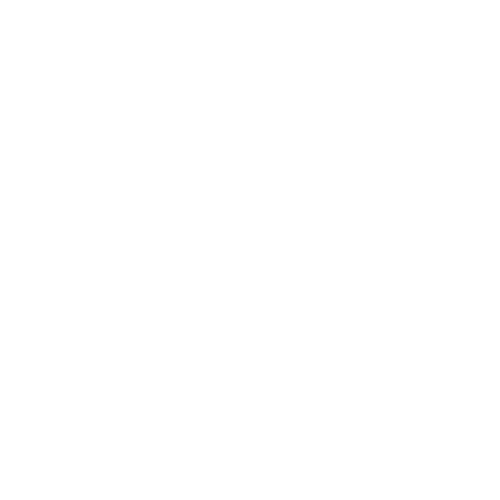
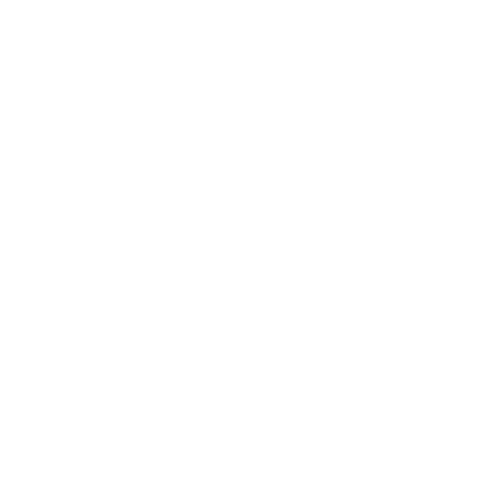
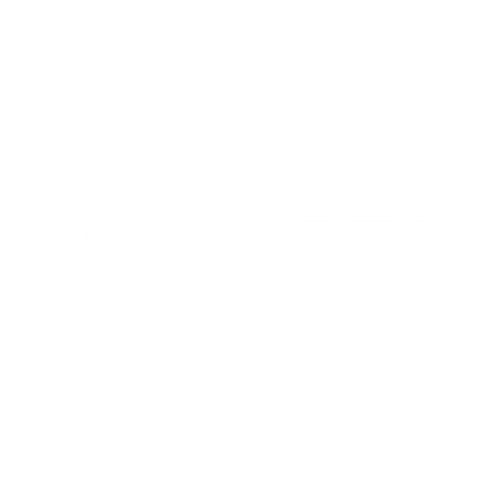
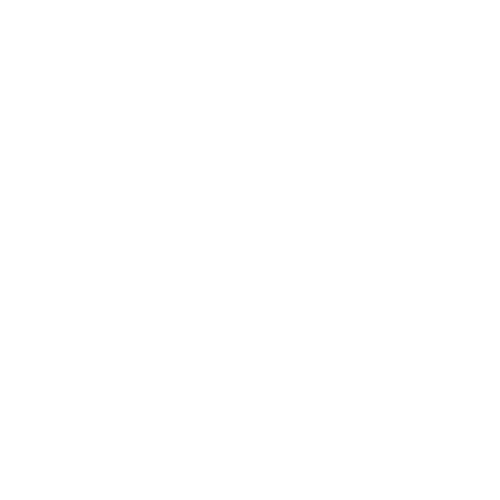
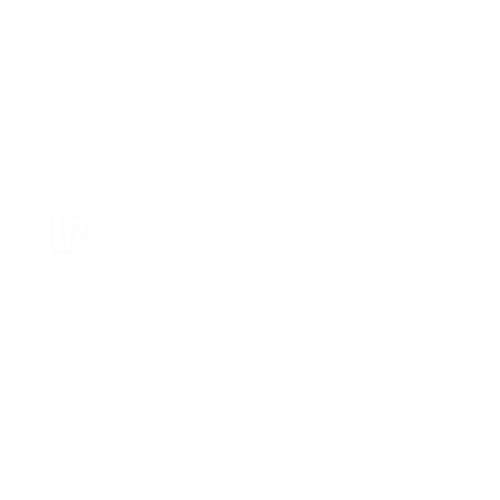